O MNĚ
Toto je můj příběh,
příběh obyčejného kluka z vesnice, co přestal truhlařit a dělá jen podlahy, jak to všechno začalo ...a jak to jde…. 🙂
Příklady mojí montáže a snahy u zákazníků ...
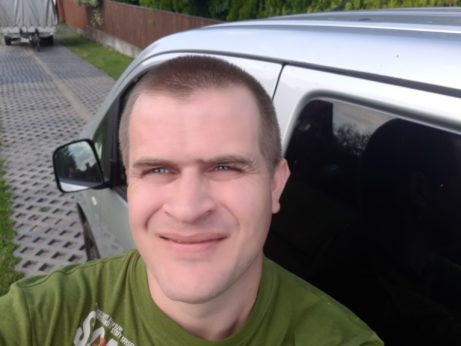
Můj příběh
Mé jméno je Radim Pollák a již 9 let se naplno zabývám výrobou autopodlah z překližky do užitkových vozidel.
Můj příběh na tomto tématu, ale začal ještě asi o 2 roky dřív, kdy jsem od známého dostal zakázku na VW T5 rozvor 3400. Požadavek zněl „do tří dnů vyrobit podlahu“ a auto mělo odjet do Chorvatska s batohy. V tu chvíli začal závod s časem – nevěděl jsem o tom vůbec nic a to i přesto, že jsem vyučen truhlářem a truhlařinu jsem aktivně provozoval. Známý mluvil o desce v hnědé barvě, kterou dávají na vleky, a od kamaráda věděl, že tam dal 12 mm tlustou. Viděl jsem ji již kdysi také v obchodě s velkoplošným materiálem, ale v praxi jsem ji nikdy nepoužil.
Moje zjištění o tom, jak začít, nebylo tak snadné, jak jsem si představoval. Po pár hodinách přemýšlení a propočítávání různých rozměrových variant mi vyšel jako optimální formát desky 1500 mm šíře, aby to bylo jen ze dvou kusů. Vyrazil jsem do velkoobchodu s deskami a snažil se najít moji vysněnou desku. V obchodě mi řekli, že na to berou občas truhláři překližku v této hnědé barvě. Zeptali se, na co to mám. Odpověděl jsem „do dodávky na podlahu“ a zeptal se, jakou tlouštku tam mám dát, co mi doporučí nebo co berou jiní? Potřeboval bych, aby to mělo 1500 mm šíře a byla mi jasná délka desky 2500 mm a také to, že do auta to v kuse asi nedám – potřebuji 2 kusy, které dám za sebou po šíři. Tloušťku na vleky prý berou 15 mm. Do dodávky – to nevíme, zněla druhá odpověď, lidé berou jen tento formát, jiný nevedeme. A stačila by vám tam asi 9mm tloušťka, zněla třetí odpověď, tu ale máme jen v šíři 1250 mm. V tu chvíli jsem začal mít první vrásky na čele a mých vysněných 1800,- Kč za práci na této zakázečce se začalo skrze čas tím strávený rozplývat. Zavolal jsem známému a informoval ho, že dvanáctku nemají. On v tu chvíli asi v duchu začal litovat, že to nehonil dříve a s tím šmrdlou to asi taky nevyhrál, když neumí sehnat ani desku (navíc tlustou 12 mm a ne 9 mm).
Když se vrátím do současnosti, musím se usmívat. Věci ohledně tlouštky a formátů desek jsou pro mě samozřejmé a z praxe vyzkoušené a musím říci, že to je nekonečný boj. Cenovku nám zpestřují výrobci desek skrze zdražení vstupních surovin, celníci clem a i Česká národní banka kurzem Eura. Velkoobchody s klasickým laminem do interiérů tímto specializovaným zbožím záměrně neumějí obchodovat a ani nechtějí naskladňovat tyto jiné formáty, natož dezény – je to pro ně nezajímavé. Zjednodušeně řečeno: sehnat někoho na shnilý starý vlek o šíři 1250 mm je jednodušší, než nahánět někoho z truhlíků, kdo udělá občas dodávku.
Určitě si pomyslíte, jaký je rozdíl mezi 1250 x 1500 šíří desky v ceně obou formátů desek? Žádný. Oba formáty jsou v těchto obchodech stejně drahé (tedy pokud je vůbec mají), ale skrze výtěžnost na tuto aplikaci obrovský. Toto moje zjištění bylo docela šokující. A až daleko později jsem zjistil, že velkovýrobci podlah kombinují oba dva typy těchto formátů desek. Vše vzniká tak, že je velkoobjednávka na daný dezén a fabrika vychrlí formát na míru, takže pro případ aplikace do dodávek je to formát 1870 délky x 1250 nebo 1500 mm šíře. Tím si značně a skrze množství obrovsky ovlivní ziskovost a výslednou cenu prořezu, dýhárna tím ušetří nastavovací procesy na lince a všichni jsou spokojeni.
Hodně výrobců překližek disponuje jen šíří lisu 1250 mm – to na kamionovou dopravu či námořní kontejnery plně dostačuje, tak proč se trápit s jiným formátem a myslet na výrobce nebo uživatele dodávek, kteří si to řeší nakonec třeba i sami? Tyto informace nejsou jenom dokladem, jestli to tak je, ale z praxe, různým poptáváním a plněním zakázek jsem k tomu dospěl za 1,5 roku při mé produkci 80 aut za rok ať s podlahami nebo obkladem boků vozidel. Samozřejmě nejsem žádný genius a spousty fíglů jsem se učil zvenku právě od těchto velkovýrobců. Všem lidem a firmám, kteří mě v tom podpořili, chci poděkovat, protože to ušetřilo moře času.
Trh v ČR jako se všemi věcmi ve srovnání s naší ekonomikou není dle mého názoru v rovnováze. Nebudu to brát ze široka, ale říkám to, co vím o tomto segmentu podlah do automobilového průmyslu. Je to klasika v České republice: buď něco pro extra bohaté firmy, nebo něco pro extra chudé firmy, a nic mezi tím. Stát dělá všechno pro to, aby tento stav dál přetrvával. Snažil jsem se najít mezi těmito všemi věcmi nějaký kompromis a je to popravdě velmi těžké. Když to srovnám se zahraničím, tak podlaha ať ve Skandinavii nebo Rakousku či Německu, kde je ekonomika o hodně napřed, to nikdo přes nějakého truhláříka, který to nějak našmrdlá, vůbec neřeší. U nás to bude ještě několik desetiletí trvat, než tento náskok doženeme. U specializovaných firem v zahraničí, které to vyřeší i vestavbou do auta nebo regálkem, to není něco neobvyklého. Nikdo nezkoumá, jaký tam má povrch, protože i ta nejdražší varianta podlahy je pro ně OK.
Není dnes už výjimkou, že pokud jezdím dálky, tak si vestavbu včetně podlahy objednám za „éčka“ přímo za hranicemi a v řadě případů to vychází skrz dodací termín a cenu výhodněji než u nás. Jediné, v čem je rozdíl, je, že to je pořád na naše poměry ekonomicky drahé skrz návratnost investice a zisku na trhu v ČR. Tento fakt způsobuje u řemesel provozovaných profesí jen na území ČR ekonomickou nenávratnost a nechuť lidí do tohoto investovat. V řadě případů při pořízení se regál nebo jiné vybavení vymontuje ze starého a zase opět dá do nového vozu – proč to lidé asi dělají? Zatím jsem neviděl například zedníka přijet s dodávkou, vybavenou vestavbou za 50 -100.000,- Kč a s nesvařenými regálky z jeklu – to není ostuda, ale fakt.
Toto popisuji proto, že to funguje i souvisí i s mým výrobkem, což je podlaha do auta. Tento fakt mi otevřel oči. Jako výrobce podlah do aut s těmito kolosy nemůžu vyhrát. Navíc mohu vytvořit jakoukoli zakázkovou věc, která pro obra pro jedno staré nebo atypické auto není zajímavá. Eliminovat, zkrátit čas a nahánění součástek (situaci, kterou jsem si také prožil), vydělat na tom přitom peníze za kratší dobu než s tou přímočarkou za 10 hodin. To je vývoj a hledání cesty 2 let, který nikdy nekončí, pořád se učím.
Pomůžu všem, kteří o to budou stát a spěchají a nechtějí investovat do nářadí či jiného drahého vybavení pro výrobu jedné podlážky do auta. Samozřejmě, že to nebudu dělat zadarmo, pravidlo „něco za něco“ funguje i u mne, ale na druhou stranu vám to ušetří nervíčky, jaké jsem prožil u svých prvních aut. Tímto se snažím o rychlost, dobrou cenu a vzhled. Moje první zakázka (VW T5), aby to k něčemu vypadalo, sežrala 12 hodin čistého času (musel jsem započítat shánění dezénů, formátů misek do auta, hliníku na kraje podlahy, spojovacích šroubů) a i samotná výroba je u T5 opravdu složitější, než například u Fiata Ducato nebo Fordu Custom. Spousta lidí si asi řekne, co tam těch 12 hodin řešil – ale …….. dodržet stejnou mezeru mezi krajem vozidla a podlahou, přitom respektovat spoj podlahy (protože u T5 to v kuse nejde dát do auta), sehnat co nejdřív nástroj, aby mi to neorvalo vrchní ochranný film, vytvořit šablonu z papíru, mít přesně dané středy misek a trefit úchytové středy v karoserii vozu a další věci okolo, to je pro toho, kdo to nikdy nedělal, opravdu těžké nacpat to do tří dnů, než auto jede pryč.
Tyto informace tady píši pro lidi, kteří si nikdy dodávku ještě nekoupili a nedovybavovali nebo nemají v k této problematice žádné informace. Můj text nemá nikomu škodit, ale shrnout fakta, co se aktuálně děje u nás.
Děkuji za dočtení řádků
Krásný den přeje Radim Pollák
MÁ VIZE
- Aby se lidé v autě cítily mnohem lépe a jistěji, díky našim výrobkům
- Dále zlepšovat rychlost vzorování, které pomáhá lidem ušetřit moře času
- Nabízet dobré zpracování, vzhled, přesnost a rychlost